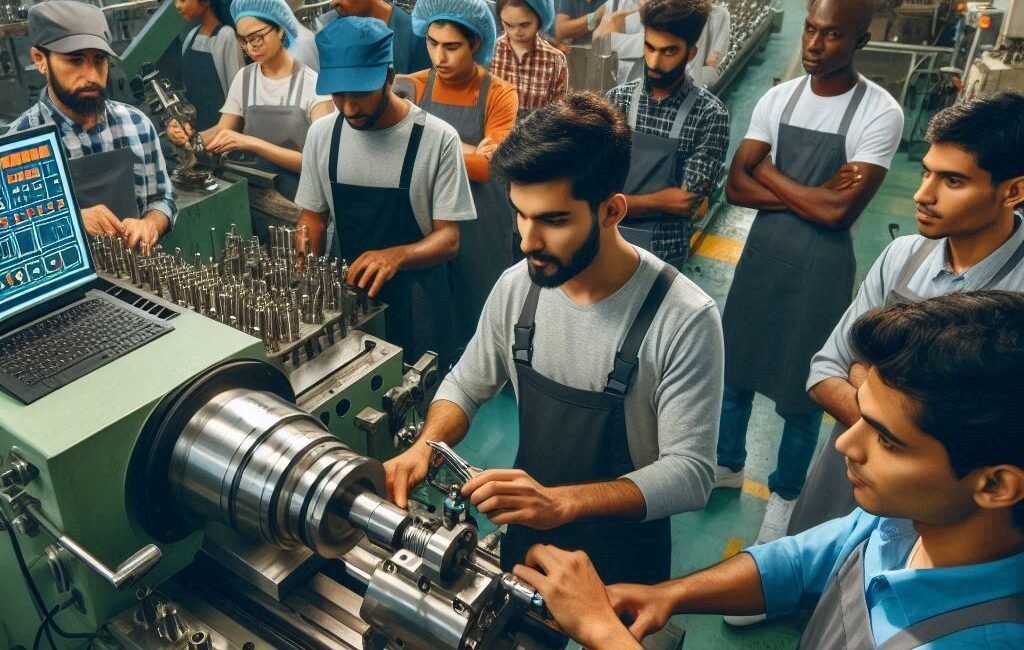
In the world of modern manufacturing, turned components play a critical role in ensuring the functionality and performance of mechanical systems. These precision-engineered parts are used across a wide range of industries, including automotive, aerospace, electronics, medical, and industrial machinery. As demand grows for high-precision, reliable, and cost-effective components, India has emerged as a preferred destination for sourcing turned parts. This article explores why partnering with a turned component manufacturer India can offer your business the competitive edge it needs.
Understanding Turned Components
Turned components are cylindrical or conical parts that are manufactured through a process known as turning—one of the most fundamental machining operations. In turning, a cutting tool removes material from a rotating workpiece to achieve the desired shape, size, and finish. This process is commonly performed using CNC (Computer Numerical Control) lathes, which ensure high accuracy and consistency in production.
Typical turned components include shafts, pins, studs, spacers, connectors, sleeves, bushings, and threaded fasteners. These components are essential for assemblies where precision alignment, smooth rotation, and tight tolerances are required.
The Rise of India as a Global Hub for Turned Components
India has rapidly gained recognition as a global manufacturing powerhouse, particularly in the field of precision engineering. With a combination of skilled labor, technological advancement, and cost competitiveness, the country is now home to hundreds of specialized suppliers offering a diverse range of turned parts.
Choosing a turned component manufacturer India gives businesses access to:
- High-quality products with strict dimensional tolerances
- Competitive pricing for both small and large volumes
- Skilled engineers and machinists with domain expertise
- Advanced CNC turning capabilities
- ISO and industry-specific certifications for global compliance
Why Choose a Turned Component Manufacturer in India?
- Advanced Infrastructure
Indian manufacturers have invested heavily in modern machining infrastructure, including multi-axis CNC lathes, Swiss-type turning centers, and automated production lines. These facilities enable the efficient production of complex turned parts with excellent surface finish and tight tolerances.
- Skilled Workforce
India is home to a vast pool of engineering professionals and technicians trained in precision manufacturing. These professionals are well-versed in international design standards and material requirements, ensuring that your components meet functional and regulatory expectations.
- Material Expertise
A reliable turned component manufacturer India can work with a wide range of materials, including stainless steel, carbon steel, aluminum, brass, copper, titanium, and high-performance polymers. This flexibility allows them to serve multiple industries with varying application needs.
- Customization and Prototyping
Indian suppliers offer end-to-end services from design assistance and prototyping to full-scale production. Whether you need a custom part developed from scratch or modifications to an existing design, Indian manufacturers can deliver fast, flexible solutions tailored to your application.
Industries Served by Turned Component Manufacturers in India
Automotive
Turned components are used extensively in the automotive industry for engine parts, transmission shafts, suspension connectors, brake components, and fuel system fittings. Indian manufacturers supply high-volume OEM parts to global automotive brands, ensuring consistency, durability, and cost-efficiency.
Aerospace and Defense
In aerospace, precision is paramount. Turned parts like fasteners, bushings, hydraulic connectors, and control system components are machined to exact specifications. Indian manufacturers with AS9100 and NADCAP certifications are now contributing to global aerospace supply chains.
Electronics and Electricals
Turned brass and copper components are widely used in electrical terminals, connectors, and sensor housings. India has a strong presence in manufacturing electrical turned parts with high conductivity and corrosion resistance.
Medical Devices
Turned components for surgical instruments, implants, and diagnostic devices require precision machining under cleanroom conditions. Many Indian manufacturers are now ISO 13485 certified and serve global med-tech companies.
Industrial Equipment
Turned parts are integral to pumps, compressors, conveyors, and automation systems. Indian suppliers offer rugged, long-lasting components for industrial applications with demanding operating conditions.
Benefits of Working with an Indian Turned Component Supplier
Cost Efficiency Without Compromise
One of the major advantages of sourcing from India is the ability to get premium-quality components at a fraction of the cost compared to Western markets. The country’s lower labor costs, optimized production processes, and raw material sourcing efficiencies help reduce total production expenses.
Global Export Capabilities
Most Indian turned component manufacturer India companies are export-ready, with experience in global logistics, documentation, and certifications. This makes it easy to establish long-term supply partnerships for international markets.
Commitment to Quality and Innovation
Leading Indian suppliers invest in quality assurance tools like Coordinate Measuring Machines (CMM), surface roughness testers, and concentricity gauges to ensure part accuracy. Some are also embracing Industry 4.0 technologies such as real-time monitoring, predictive maintenance, and digital twins to enhance performance and productivity.
Short Lead Times and On-Time Delivery
With streamlined supply chains, just-in-time manufacturing models, and responsive production planning, Indian suppliers can handle both urgent orders and high-volume projects with efficiency.
How to Select the Right Turned Component Manufacturer in India
When choosing a supplier, consider the following:
- Experience and track record in your industry
- CNC and conventional turning capabilities
- Certifications like ISO 9001, IATF 16949, or AS9100
- Quality control processes and inspection equipment
- Material sourcing and traceability
- Prototyping and design support services
- Ability to scale production as your business grows
It’s also beneficial to request sample parts, conduct audits (virtual or physical), and evaluate past client reviews and export performance.
The Future of Turned Component Manufacturing in India
India’s manufacturing sector is evolving rapidly, fueled by initiatives like “Make in India,” increased foreign direct investment (FDI), and government-supported incentives for exports and infrastructure development.
As global industries shift toward electric mobility, renewable energy, and smart automation, the demand for customized, lightweight, and complex turned components will continue to grow. Indian manufacturers are ready to meet this demand by adopting new materials, tighter tolerances, and data-driven production systems.
With a focus on sustainability, lean manufacturing, and global integration, the future is bright for any business that partners with a reliable turned component manufacturer India.
Conclusion
Turned components are the backbone of many critical systems — and their accuracy determines the efficiency, safety, and performance of end products. By choosing a trusted turned component manufacturer India, businesses can access high-precision, cost-effective, and scalable solutions that meet international quality standards.
Whether you’re looking to optimize your supply chain, reduce costs, or accelerate innovation, Indian turned component suppliers offer the ideal combination of engineering capability, global reach, and customer focus. Partner with India’s best, and take your manufacturing to the next level.